In recent years, the construction industry has witnessed a significant paradigm shift with the advent of modular construction. This innovative building technique, also known as off-site or prefabricated construction, is gaining traction globally for its efficiency, sustainability, and cost-effectiveness. In this article, we explore the key aspects of modular construction and its transformative impact on the traditional building process, looking at leading players in the industry such as LINQ, part of the ALEC group, and DuBox and DuPod, part of Group AMANA.
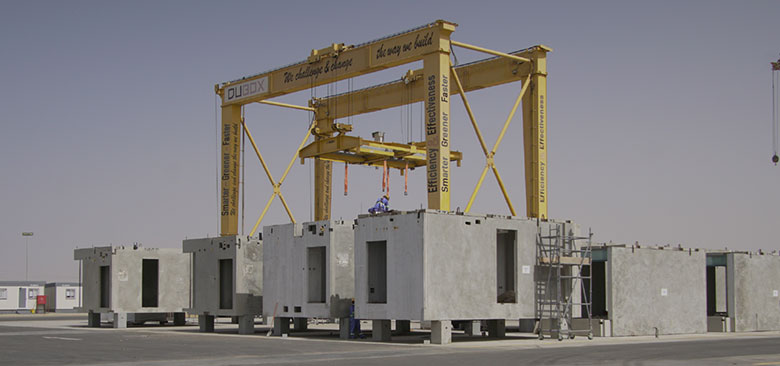
Defining Modular Construction
Modular construction involves the creation of building components or modules in a controlled factory environment, away from the actual construction site. These modules, often complete with walls, floors, ceilings, and even fixtures, are then transported to the site for assembly. The assembly process is akin to piecing together a puzzle, with modules interlocking seamlessly to form the final structure. In Saudi Arabia, blue-chip companies such as AMANA, ALEC, and Spacemaker are all pushing back the boundaries in modular construction to provide clients with solutions that are timely, sustainable, quality-led, cost-effective, and versatile when it comes to design parameters.
This approach is perfect for the many giga-projects that are now under development, such as Qiddiya, The Red Sea, and NEOM. Modular construction is a desirable alternative for these projects since they frequently call for the rapid construction of a significant number of buildings and infrastructure.
This approach is perfect for the many giga-projects that are now under development
At Sindalah, for instance, two ALEC companies provided their unique breadth of expertise: LINQ, which specializes in providing top-quality manufactured modular hotel solutions, and AES, which provides turnkey building envelopes for a broad portfolio of bespoke and complex projects.
The LINQ factory runs six modular production lines in a fully controlled environment that is well-ventilated and out of the sun. Many other modular manufacturers don’t have facilities like these and have to work outside, contending with summer working hours and other related challenges, so in terms of productivity, LINQ has the ideal facilities.
Renowned for its innovation and creativity, LINQ has utilized a completely dry system at Sindalah with an innovative and eco-friendly product, a board made of date palms. Graham Petty, Operations Manager at LINQ, explained: “Whenever we can, we use sustainable materials. For Sindalah, we suggested to NEOM that we use sustainable date palm board because we were trying to avoid using concrete because of the not-insignificant amount of emissions it produces. Utilizing completely dry construction also helps with our production sequencing because it means we don’t have to wait for the concrete to cure, determining that the production line moves faster.”

LINQ’s sister company, AES, has also been active at Sindalah, with its in-house façade designers and engineers bringing architectural concepts to life. Presently, AES is working on two major projects for NEOM, the iconic Sindalah Gold Course Clubhouse and the installation of a state-of-the-art façade for 11 modular buildings for Marriott Hotels.

Micael Quinn, Operations Manager at AES, says: “The state-of-the-art façade will feature a multi-layered approach, beginning with a highly insulated and waterproof sandwich panel. This will be seamlessly clad with a leather-coated Glass Reinforced Plastic (GRP) panel both internally and externally, creating a distinctive aesthetic that harmonizes with the natural beauty of the surroundings.”
Construction timelines can be shortened by up to 50%
Completed 30% Faster
DuBox, a division of AMANA, is another company that leads the field in offsite manufacturing construction in the GCC, delivering reduced costs, increased quality, faster completion times, and a sustainable construction model. Nearly 85% is designed, manufactured, and assembled offsite in a controlled environment at a DuBox factory before traveling by road to the project site.
Numerous savings have been made; a 30% reduction in labor costs; a 50% – 90% reduction in overall waste and a 30% reduction in solid waste. The project will be completed 30% faster than traditional construction, producing numerous environmental, HSE, and economic benefits.
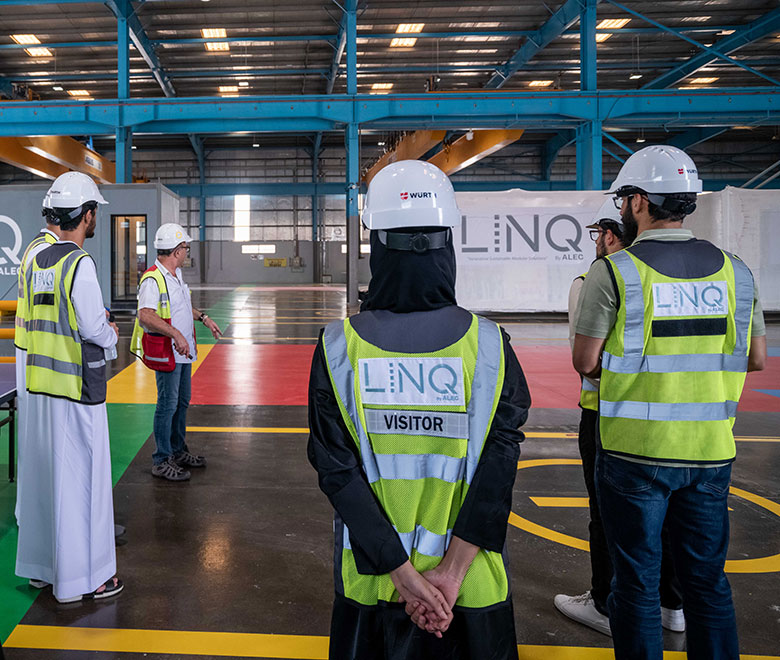
At AMANA, all QA and QC processes and inspections are completed in its production bays throughout the manufacturing process to ensure consistent quality. DuBox follows a double testing procedure, in the factory and on-site once the modules are assembled, ensuring only the highest quality manufactured product is delivered to the client, with an AMANA spokesperson saying: “The modules undergo flood testing to ensure water tightness and MEP pressure testing in the factory before dispatch. This enables any rectifications required to be conducted in a factory environment rather than during the traditional on-site works.”

The modular construction process is characterized by meticulous precision and quality control
Modular construction aligns with the growing emphasis on sustainable building practices too. The controlled environment of the factory allows for meticulous resource management, reducing material waste. Additionally, the reduced on-site construction time translates to less disruption to the surrounding environment and communities. As the construction industry seeks greener alternatives, modular construction emerges as a promising solution to minimize its ecological footprint.
The AMANA spokesperson said: “At AMANA, we prepare a Construction Environmental Social Management Plan (CESMP): It lists environmental management controls required for the work to be carried out under the contract, and environmental management tasks such as reporting, inspections, and training. The objectives of this CESMP are to identify the potential environmental impacts that can result from the planned construction activities and identify measures to control or avoid these impacts.”
Shorter construction timelines mean fewer labor hours, reduced financing costs, and earlier occupancy
Precision and Quality Control
The modular construction process is characterized by meticulous precision and quality control. In a factory setting, each module is constructed to exact specifications, ensuring consistency and accuracy. This precision is often challenging to achieve on traditional construction sites where variations can occur due to weather, human error, or other external factors. The strict quality control measures inherent in modular construction contribute to buildings with higher structural integrity and uniform quality.
While the initial perception may be that modular construction is more expensive, the overall cost-effectiveness becomes evident when considering the reduced construction time and increased efficiency. Shorter construction timelines mean fewer labor hours, reduced financing costs, and earlier occupancy, translating into substantial savings. Moreover, the controlled factory environment minimizes material waste, optimizing resource utilization and further contributing to cost-effectiveness.
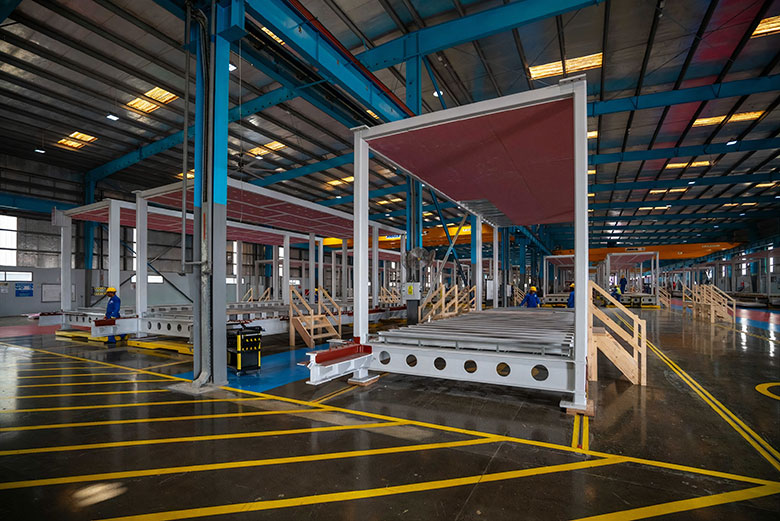
Moreover, contrary to the misconception that modular construction leads to cookie-cutter buildings, this method offers considerable versatility in design. Architects and designers can create diverse and aesthetically pleasing structures by combining various modules. From residential homes to commercial spaces and educational institutions, the adaptability of modular construction allows for a broad spectrum of design possibilities, meeting the diverse needs of different projects.
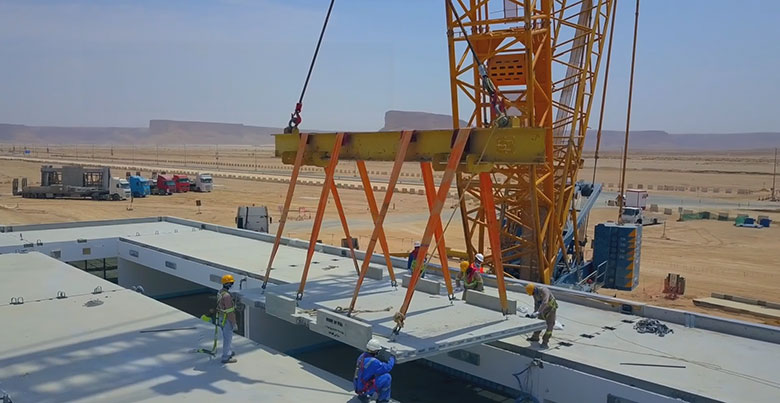
Challenges and Considerations
While modular construction offers numerous advantages, it is essential to acknowledge the challenges associated with this innovative approach. Transportation of large modules to the construction site requires careful planning, and site logistics must be well-coordinated to ensure smooth assembly. Additionally, some traditional construction stakeholders may initially resist the shift to modular methods, emphasizing the importance of industry-wide education and collaboration.
Conclusion
Modular construction stands at the forefront of a transformative era in the building industry. Its efficiency, sustainability, cost-effectiveness, and versatility make it an appealing choice for developers, builders, and architects worldwide. As technology advances and the demand for more sustainable building practices increases, modular construction is poised to play a pivotal role in shaping the future of the construction landscape, enabling the digitalization of design and construction processes, which is a stepping stone to industrializing construction. The success stories of projects embracing modular construction underscore its potential to revolutionize the industry and provide a blueprint for a more efficient and environmentally conscious approach to building.
Group Amana