Developers around the world are increasingly turning to modular construction to meet the demand for new buildings; a demand caused by more people living in established cities and new mega and giga-projects that seek shorter construction times and accelerated project commercialization.
In Saudi Arabia, the industry has been exploring a variety of innovative construction methods, with modular building being seen by many as a viable solution to address the Kingdom’s growing requirement for a range of building types and its ambitious infrastructure projects.
Customizable Creations, Infinite Possibilities
In recent years, Saudi Arabia has witnessed tremendous urbanization, resulting in increasing demand for housing, commercial buildings, and infrastructure. Modular building provides a more effective and speedier approach to address this need, with off-site manufacturing and assembly potentially reducing construction time and labor costs quite significantly.
This approach is ideal for the wide array of giga-projects currently in development, such as NEOM, The Red Sea, and Qiddiya. These projects often require a large volume of buildings and infrastructure to be constructed quickly, making modular construction an attractive option.
Similar to many other countries, Saudi Arabia also faces a shortage of affordable housing, and modular construction can play a pivotal role by providing cost-effective and efficient solutions.
And of course, modular construction aligns perfectly with the Kingdom’s growing focus on sustainability and green buildings, as it helps to reduce waste, conserve energy, and encourage eco-friendly materials.
The Saudi government, construction companies, and developers in the Kingdom are constantly exploring new, innovative, and advanced construction methods, including 3D printing for buildings, an area that could become of increasing interest to one of the fast-growing and most ambitious countries in the world.
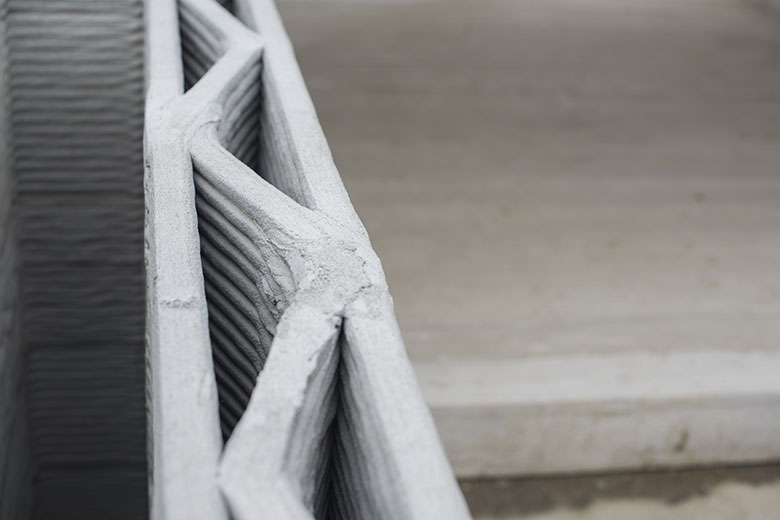
It is the world’s largest on-site 3D printed building and took just 26 days to build
Embracing the Future with 3D Printing
The saying is that necessity is the mother of invention, and this could be nowhere more true than in Saudi Arabia.
Back in 2021, Dar Al Arkan, the leading real estate company in the Kingdom, announced the introduction of 3D Construction Printing (3DCP) technology in Saudi Arabia. Partnering with the Construction of Buildings on Demand (COBOD), a leading manufacturer of construction 3D printers, for this initiative, the company pioneered the transition of the industry toward advanced and sustainable building practices, and in doing so, complemented the goals of Saudi Vision 2030 to support economic diversification and digitization.
Unlike traditional building methods, 3DCP can cut the construction time by more than half, as well as requiring less manpower, since it takes only three workers to build an entire house. Naturally, this then contributes to decreased lost time injuries, creating a safer workplace. In addition, less concrete is needed to complete a building, thus making the technology more sustainable and a practical solution for the low-carbon construction industry of the future.
Dar al Arkan produced the first villa printed directly on-site, too. This was achieved without any cooling equipment or shade, denoting that the technology can be used to erect homes right through the year regardless of weather conditions. The villa, built in Shams Al Riyadh, made use of locally made materials, including cement, sand, rocks, and stones, with varying degrees of concentration, to ensure the structure was up to four times stronger than conventional construction.
Amongst its many features, the villa incorporates nine solar panels to power its heating and lighting and a series of IoT/smart tools for doors, locks, air conditioning, and more. Heat-reflecting ‘nano-technology’ was used to coat the exterior of the structure, rendering it up to 40% more heat-resistant than traditional buildings. It is the world’s largest on-site 3D printed building and took just 26 days to build. It is compliant with all relevant building codes.
This project did not go unnoticed by the local authorities, with the Ministry of Housing commenting: “In Saudi, we are rapidly developing in the construction sector through our Building Technology Initiative and implementing new technologies to enable 70% of the Saudi population to own their homes by 2030. Our strategy is to revolutionize the way people think about home through smart futuristic methods.”
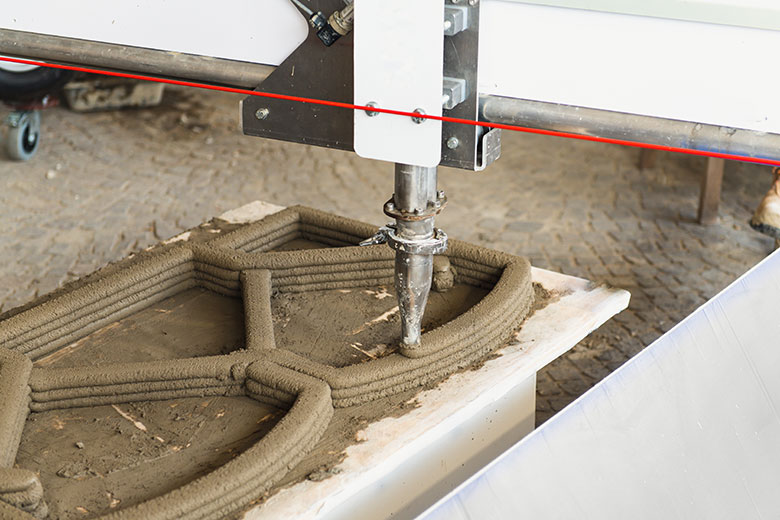
A number of 3D printing materials are manufactured from recycled or environmentally friendly resources
Efficiency Redefined
In spite of the countless advantages of 3D construction, there are still certain challenges, for example, the cost of 3D printing technology is still quite high, making it less accessible to many construction companies. However, although still an emerging technology, with further development and investment, it has the potential to revolutionize the construction industry, offering various benefits and exciting possibilities, including
Speed
When compared to traditional methods, 3D printing for buildings can dramatically reduce construction time. It allows for the rapid fabrication of building components, which shortens the entire timeframe.
Cost-Effectiveness
While the initial investment in 3D printing technology can be significant, the reduced labor and construction time can result in long-term cost reductions.
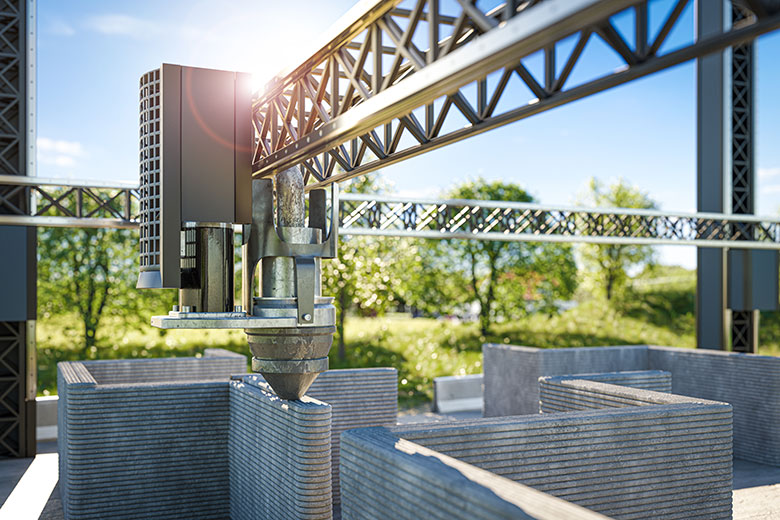
Design Flexibility
3D printing enables stylish and unique architectural designs that would be impossible or too costly to realize using standard construction methods.
This approach is ideal for the wide array of giga-projects currently in development, such as NEOM, The Red Sea, and Qiddiya
Sustainability
A number of 3D printing materials are manufactured from recycled or environmentally friendly resources, lowering the environmental impact of construction projects. Furthermore, precision material installation helps reduce waste during the construction process.
Safety
Much of the construction work can be automated with 3D printing, decreasing the need for human labor in dangerous locales.
The actual process itself involves placing layers of construction materials on top of each other, progressively building up the desired structure. Subject to the particular 3D printing technique, an assortment of materials can be used, including concrete, cement mixtures, polymers, and even recycled materials. Sophisticated 3D printers can extrude these materials in accurate shapes and patterns according to digital blueprints, permitting multifaceted and customized designs.
Modular Innovations Unleashed
There are several different applications for 3D printing within the construction industry, in addition to building entire structures. 3D printing is, for instance, ideal for creating prototypes and scale models, allowing architects and engineers to visualize their designs before constructing the final building. It is also perfect for fabricating complex and non-standard building components, allowing for the creation of complicated structures that would be challenging using conventional methods.
3D printing can assist in generating custom components for building renovations and retrofitting projects too, and in the aftermath of natural disasters, it can be used to rapidly construct temporary shelters and emergency housing.
Indeed, as the technology continues to advance and gain wider acceptance, 3D printing for buildings has the potential to reshape the construction industry, making it more efficient, sustainable, and adaptable to assorted architectural designs and housing needs.
Not just 3D printing either, but modular buildings in general, which are created in a factory-controlled environment. This allows for greater precision, efficiency, and quality control during the manufacturing process, as well as being up to 50% or more faster than traditional construction. And as for cost, although the upfront costs are a little higher due to the need for specialized factories and transportation, the overall cost of modular construction can be lower than conventional construction due to reduced labor, less waste, and faster completion.
Add this to the fact that factory-based construction ensures better quality control, as each module is built to exact specifications and undergoes rigorous inspections before leaving the factory, and reduced site disruption since most of the construction occurs off-site, and modular buildings are most definitely a solution to future needs.
Transforming Spaces, Simplifying Lives
Contrary to the misconception that modular buildings are all the same, they can be customized to meet the specific needs and design preferences of clients, resulting in the most stylish and unique villas, schools, commercial spaces, and social housing.
On a global scale, with the world’s population growing faster than ever and the housing industry being unable to keep up with demand, modular construction could be the remedy we’ve all been looking for. House prices are going through the ceiling, and people on low wages find it hard to pay their rent, let alone save a downpayment for a house. Modular construction may well have the ability to change this. By making house construction much more economical without sacrificing quality, house prices could shrink, transforming the market and providing more people with their own homes.
With modular construction, we have a blank canvas to make environmentally friendly, attractive buildings at a much lower cost. For developers and general contractors, there is swifter project execution, higher margins, and greater competitiveness. Meanwhile, the industry can take advantage of modular practices to create more reasonably priced housing on safer, smaller construction sites. And that could deliver good jobs for a wider skill base than traditional projects can accommodate. It’s a win-win for everyone!