Off-site manufacturing, also known as prefabrication or modular construction, has emerged as a transformative force in the construction industry, revolutionizing traditional building practices and unlocking new opportunities for efficiency, sustainability, and innovation. This approach involves the fabrication of building components or entire modules in a controlled factory environment, away from the construction site, before transporting and assembling them onsite, with DuBox, an AMANA company, leading the field in the GCC, delivering reduced costs, increased quality, faster completion times and a sustainable construction model.
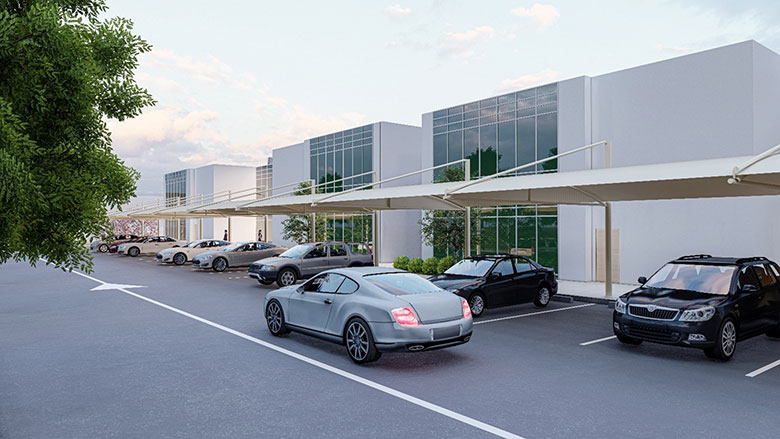
Active on major giga-projects for blue-chip clients such as AMAALA and NEOM, DuBox is unlocking new efficiencies, driving greater value, and creating buildings that are better designed, built, and operated. Nearly 85% of projects are designed, manufactured, and assembled off-site in a controlled environment at a DuBox factory before traveling by road to the project site. Each module is built in pre-cast concrete and is fully constructed and fitted out, including all MEP work, before reaching the site. QA & QC processes and inspections are completed in our production bays throughout the manufacturing process to ensure consistent quality.
Off-site construction commences before the site is ready and it takes place in parallel to site clearance, landfilling, and substructure works. This is fuelled by the company’s use of volumetric concrete, with materials such as aggregates, cement, water, and additives being batched and mixed on-site rather than at a centralized plant. This process involves using volumetric concrete mixers, which are specialized vehicles equipped with separate compartments for storing and proportioning the raw materials.
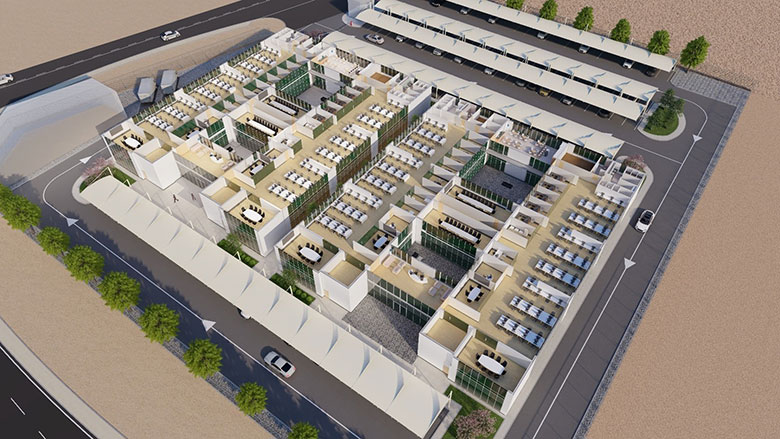
This, along with other innovations, has seen DuBox make numerous savings; a 30% reduction in labor costs; a 50% – 90% reduction in overall waste, and a 30% reduction in solid waste. Projects can be completed 30% quicker than traditional construction, producing several environmental, HSE, and economic benefits.
By shifting the site activities off-site and, due to the innovative system DuBox brings to developers, by default it is able to achieve LEED/MOSTADAM ratings.
Each module is built in pre-cast concrete and is fully constructed and fitted out, including all MEP work
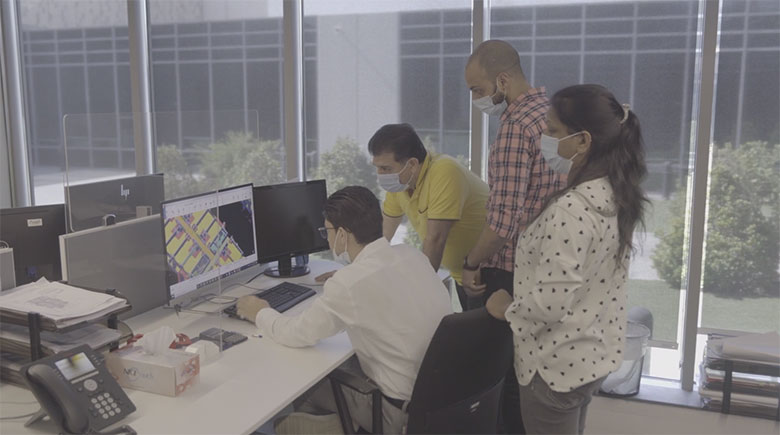
Integrating Technology for Enhanced Efficiency in Modular Construction
Digitalization lies at the heart of everything that DuBox undertakes; from design to execution, all processes are operated on cloud-based platforms.
BIM technology allowed DuBox to design and integrate all of NEOM’s delivery team with engineers in different offices and countries to design and build in real-time as both design and construction progressed, enabling it to deliver the project in record time.
The planning of activities for this project involved a team of multiple engineers engaging virtually on a concept, design, and execution plan, considering successes and many lessons learned from previous projects in the DuBox database. Planned completion of engineering and procurement tasks before commencing the off-site construction was crucial to avoid any delay.
The project will be completed 30% quicker than traditional construction
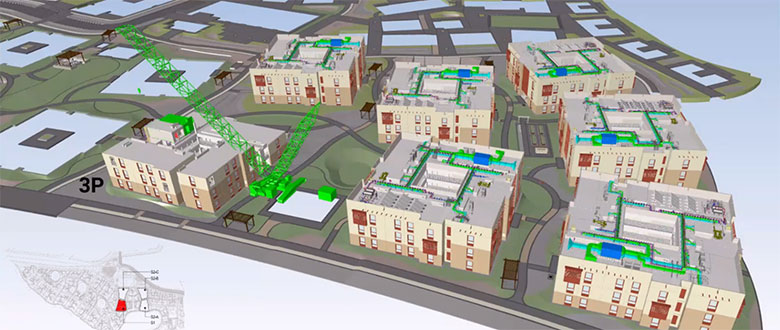
Striving for Perfection through Total Quality Management
By shifting construction activities to a controlled factory setting, projects can benefit from improved productivity, enhanced quality, and reduced labor costs. The assembly-line production of building components allows for greater precision and standardization, minimizing waste and rework. Additionally, the ability to work concurrently on multiple modules or components can dramatically shorten project timelines, enabling faster delivery and occupancy of buildings.
Indeed, guided by a relentless pursuit of excellence, DuBox pioneers transformative solutions that redefine the industry, engineering tomorrow’s breakthroughs today. Embracing challenges as opportunities, the company has delivered 3,635 modules to KSA and 9,627 modules to the wider GCC region since its Rabigh yard was established in 2019. At present, 1,160 modules are in production, with the yard turning out 16 modules per day (800m2).
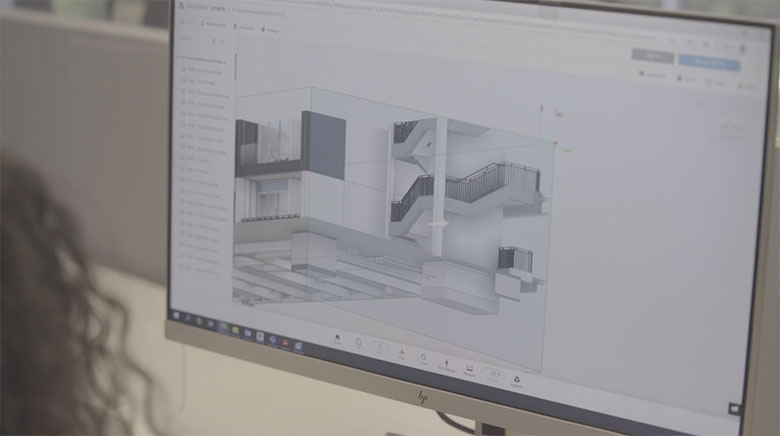
DuBox is also committed to ‘parallelism’, thus reducing overall duration, optimizing resource utilization, and minimizing the idle time between tasks. “This ensures that we can work on several floors at the same time while the site is being prepared to receive the modules,” explains Jihad Bsaibes, CEO at Group AMANA: “Investment in bespoke mega-cranes, co-designed with leading European manufacturers, will lead to further automation and an increase in production, allowing DuBox to continue to support the ambitions of Vision 2030.”
These cranes are more than 20 meters in height and enhance AMANA’s continuous improvement to industrialize construction. They are currently 85% manufactured and will be en route for operational use in H2 of 2024.
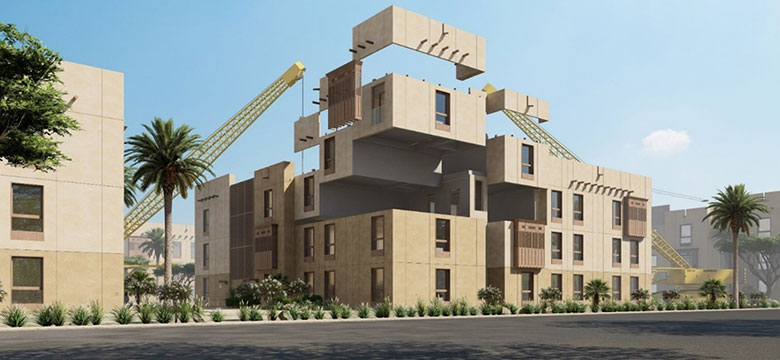
Factory-Quality
QA & QC processes and inspections are completed in DuBox’s production bays throughout the manufacturing process to ensure consistent quality. The company follows a double testing procedure in the factory and on-site once the modules are assembled, ensuring the highest factory-quality product is delivered to the site.
In addition to efficiency and quality benefits, DuBox off-site manufacturing offers environmental advantages that align with sustainability goals. The controlled factory environment allows for better management of resources and waste, with opportunities for recycling and reuse of materials. Furthermore, the precision engineering and modular design inherent in prefabrication enable optimization of building performance, including energy efficiency and thermal comfort. As sustainable building practices become increasingly important in addressing climate change and resource depletion, DuBox provides a viable solution for reducing the environmental footprint of the construction industry.
BIM technology allowed DuBox to design and integrate all of NEOM’s delivery team with engineers in different offices and countries
Off-site manufacturing also fosters innovation and customization in building design and construction. Advanced technologies such as Building Information Modeling (BIM) and robotic automation enable architects and engineers to explore creative design solutions and optimize building performance. The modular nature of prefabricated components allows for greater flexibility and customization, accommodating diverse architectural styles and functional requirements. This versatility opens up opportunities for architects, developers, and building owners to realize their vision while maximizing efficiency and cost-effectiveness.
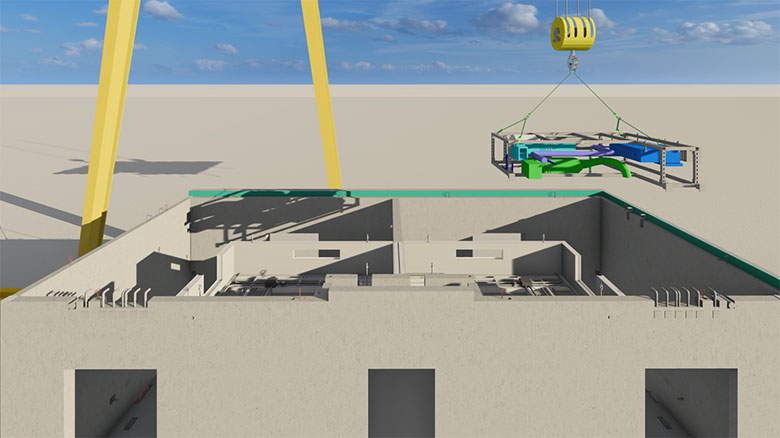
Proactively Ensuring Quality in Product Development and Manufacturing
Continuous R&D in the box design and handling is core to DuBox’s culture of innovation, and this is reflected in the lessons learned and feedback of its clients, allowing it to strive for continuous improvement in its efforts to ‘productize’ its construction delivery to the market.
In addition to efficiency and quality benefits, DuBox off-site manufacturing offers environmental advantages that align with sustainability goals
DuBox off-site manufacturing represents a paradigm shift in the construction industry, offering a host of benefits including speed, cost-effectiveness, quality, sustainability, and innovation. As the demand for faster, smarter, and more sustainable construction solutions grows, prefabrication is poised to play an increasingly prominent role in shaping the built environment of the future. By embracing off-site manufacturing techniques, stakeholders across the construction value chain are enjoying efficiencies and quality enhancements that are setting a new benchmark for the entire industry.
Group Amana