What are the circumstances that result in disruption in the construction industry, and how do you provide a practical approach to undertake a credible disruption analysis. We spoke to HKA’s Pramod Oommen, who has over 20 years of work experience in the construction sector, the last nine solely as a delay analyst on prolongation and disruption claims.
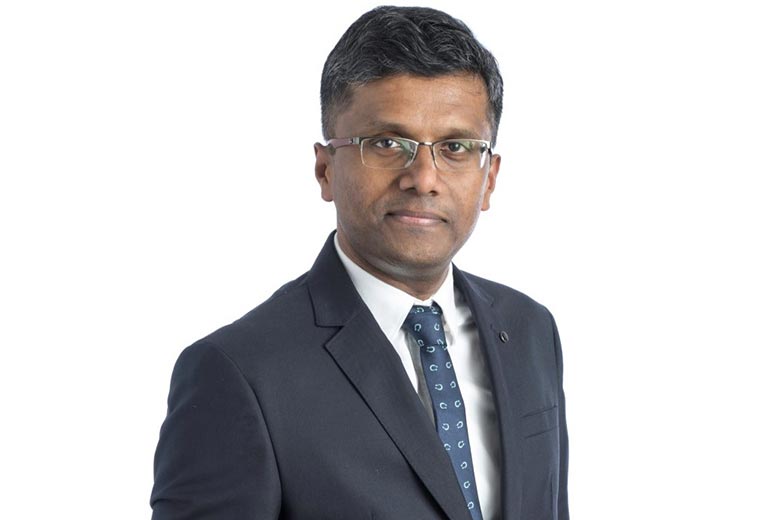
Saudi Projects: What is disruption in construction?
Pramod Oommen: Construction practitioners commonly use the term ‘disruption’ to refer to a loss of productivity caused by unanticipated interruptions to the progress of works. The usual consequence is a reduced rate of work efficiency, which leads to an increase in direct hours spent (labor and/or equipment) on the relevant disrupted work. If disruption is caused by the employer, the contractor has entitlement to seek compensation for loss of disrupted labor and equipment hours. It is not unusual even in such cases for a portion of disrupted hours to be attributable to the contractor.
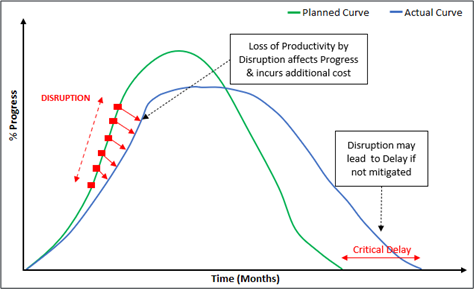
SP: So it is when a project is delayed?
PO: Disruption and delay are based on two different concepts; however, it is common to refer to claims as ‘delay and disruption’ as though to suggest they are the same. A delay relates to lateness in completion of the works or portion thereof (i.e., either critical or non-critical delays), while disruption refers to loss of productivity to specific works undertaken.
However, it is possible for delay to cause disruption and vice versa. Hence, by way of example, repeated disturbances to the planned work cause disruption, which could result in delays:
SP: How do you measure disruption?
PO: When labor and equipment costs exceed the planned value, a disruption claim is a plausible solution to recover costs for lost productivity in performing the works. However, it is prudent to consider whether the contractor’s plan (budgeted values) to perform the works were realistic; if flawed, the planned effort cannot be relied upon as a valid yardstick against which to measure the effect of disruption. In such circumstances, a comparison between the actual effort required to complete the works when disruption is not present (referred to as the ‘measured mile’) against the actual effort taken to complete the works when those works were negatively affected (i.e., when disruption was present) is likely to be more appropriate.
Any disruption claim is challenging to prove without the support of actual records, if absent, any perceived losses on labor or equipment costs may be attributed to the contractor’s own failures to perform the works.
Here, productivity refers to the efficiency level of labor and equipment, which can be measured either for labor, hours, equipment (plant hours) or cost (price per unit). Hence, the failure to keep records for actual manhours (or costs) expended to perform the works with reduced productivity could prove detrimental to a disruption claim.
When labor and equipment costs exceed the planned value, a disruption claim is a plausible solution to recover costs for lost productivity in performing the works
SP: So, how do you evaluate delay and disruption?
PO: When evaluating delay, the contract terms may provide rules or guidance on methodology and qualifying relevant event(s) that caused delay. On the other hand, for disruption, the contract terms are seldom useful. In disruption claims, the contractor should provide evidence regarding:
- The trade/progress of work which was disrupted
- Impacted (when disrupted) and unimpacted period(s) on work
- Additional manpower (and equipment) expended on disrupted trades
- Evaluate the difference between the periods analyzed
- The cause (events) which caused disruption to work
Therefore, it is of vital importance for the contractor to maintain a site log for works carried out for the duration of the project. It will allow the contractor to measure the productivity of works carried out at any given point in time. In such cases, it would be possible for the contractor could take remedial measures whilst being subject to disruption, raise notices of disruption to the employer, or as a last resort, make a credible claim to seek disruption costs. It is imperative for the contractor to maintain site records to show how the works were undertaken during impacted and unimpacted periods, and preferably for the whole project period. In summary, the key to any successful disruption claim is records, records and records.
Commonly used methods to measure disruption in construction are:
- Baseline productivity analysis
- Earned value analysis (EVA)
- Measured mile analysis
SP: Is disruption difficult to establish or quality?
PO: It has been widely accepted that disruption is difficult to establish, substantiate or quantify. However, this is not entirely true and is largely due to the contractor not maintaining proper and sufficient site records. In most cases, disruption is usually not identified or alerted as it occurs; it is only when the contractor has found a significant difference between its planned and actual labor and plant costs that are unaccounted for by any variations issued by the employer or the contractor’s own inefficiencies.
In summary, disruption involves a situation where, as a consequence of events attributable to the employer, the contractor’s labour and plant productivity were substantially reduced, resulting in the contractor having to burn additional labor and plant costs to carry out the works.
Any disruption claim is challenging to prove without the support of actual records
SP: Where does a company stand in strictly legal terms?
PO: It is likely that disrupted works relate to sub-critical delays which are not part of critical path analysis (i.e., critical delay) with delays to project completion. As a result, securing a time extension claim (EOT) will not help to recover disruption losses associated with the specific sub-critical trades. In simple terms, EOT deals with indirect resources, those which are required for the extended project period, while disruption deals with direct resources which worked in a disrupted manner. The Hudson’s Building and Engineering Construction Contracts states:
- “The distinction between delay and disruption is important but rarely articulated and is to an extent a matter of definition. Delay is usually used to mean a delay to the completion date, which presupposes that the activity which was delayed was on the critical path. Disruption to progress may or may not cause a delay to overall completion, depending on whether the activity delayed is on the critical path as explained above, but will result in additional cost where labour or plant is under-utilized as a consequence of the event.”
In the Walter Lilly case, Mr Justice Akenhead suggested three elements that will help support a contractor’s disruption claim.
- Events that entitle it to loss and expense
- Identifying the events which caused disruption
- That disruption caused loss and/or expense to the contractor
The contractor’s failure to adhere to the notice provisions within the contract can result in rejection of the disruption claim, especially in contracts with time-bar provisions. In Van Oord and another v Allseas UK Ltd case, the disruption claim was rejected wherein the contractor failed to submit notices. However, in Obrascon Huarte SA v Her Majesty’s Attorney General for Gibraltar, the judge did not take an isolated view of the time-bar clause wherein the breach by the employer was obvious to him. It is good practice to submit relevant notices to prevent disruption claims being time-barred and provides strong evidence that an event had occurred. The consequences of the event could be disputed, but the record of the event should never be in question. In addition, the contractor must have a legal entitlement under the contract, i.e., the disruption event must typically have been caused by an act omission or default by the employer.
The current performance of work can be used to forecast cost or schedule overruns in a project by making use of trend data
SP: What aspects should one look at to prove a disruption claim?
PO: The causative agents that result in disruption to construction work are numerous. The causes may include irregular work patterns, densely populated workspaces, extended working hours, lack of quality supervision, poor communication between workers, frequently performing out-of-sequence work, delayed responses to request for information (RFIs), shortage or delayed material deliveries, lack of required approved shop drawings, inclusion of varied works, etc. A project may finish on time but may have experienced a reduction in expected labor and equipment productivity. The effect of disruption or the loss of productivity is quantified as the difference between the planned (or actual unimpacted; in case of the measured mile approach) rate of production and the actual rate of production in the disrupted period.
SP: But how can one judge performance?
PO: The current performance of work can be used to forecast cost or schedule overruns in a project by making use of trend data. The budgeted hours to carry out the activities are compared to the actual manhours spent for the work progress achieved (work done). As work activities are progressed, manhours are earned against actual manhours which were spent by the contractor to achieve this work. In simple terms, the earned value (‘EV’) measures the manhours earned based on work done, while the actual cost (‘AC’) tells us how much was spent to do this work.
The ratio of the two terms will provide us with the cost performance index (‘CPI’). Any work with CPI less than or equal to ‘1’ indicates that actual costs are less than the earned value (positive cost variance) while CPI greater than 1 indicates that value spent is lost (negative cost variance). In the figure below, CPI value of ‘0.86’ implies that for every dollar spent, only $0.86 was earned. In this case, the cost variance is the delta between EV and CV, i.e., 30 – 35 = 5.
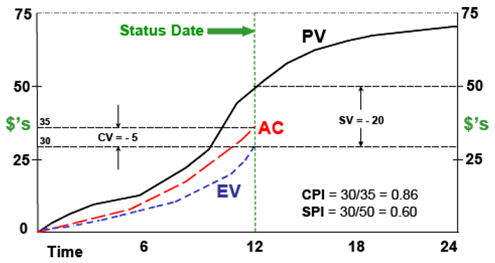
In a real case scenario, the earned value analysis (‘EVA’) must be undertaken as a minimum of four steps which are illustrated with the help of the figure below. Here, the green line shows the planned curve (budgeted hours for excavation works), the golden line is the actual hours burnt to perform the works, whereas the blue line is the earned hours based on actual progress achieved for works done. For disruption analysis, the comparison is always between the blue and golden lines and never with the green line, which shows the planned effort required to complete this work. The planned curve has no relevance to disruption analysis except to rely on the budgeted hours to arrive at the earned value. The light blue curve shows the actual cumulative progress (based on earned hours) of the works over a period of time.
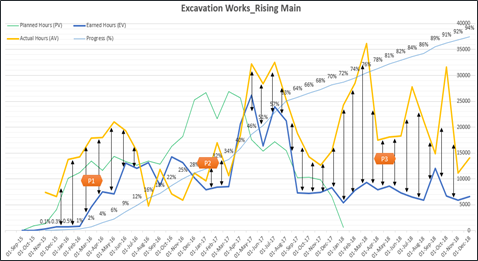
The first step is to plot the earned and actual curves for the disrupted trade, which must be identified. As can be seen, the two curves will lie in the same time period to imply that a direct comparison is possible between what was achieved (earned) and what was spent (actual) to perform the work.
The second step is to isolate time periods that were likely to be disrupted by a relevant cause(s). i.e., the disruption event. In our case, we have identified three periods (P1, P2, P3), where disruption was in play, i.e., identify periods with delta (gap) between the earned and actual curves. The delta would imply the contractor had to spend actual hours in excess of the earned value to achieve the same quantum of work, i.e., to imply that the contractor had worked in an unproductive manner to perform the works
The third step is to identify events that are likely to have caused disruption within the three time periods. If no such events are available, the disruption is likely to have been caused by contractor issues related to the learning curve, unskilled workers, delayed materials resulting in idling manpower or simply because the budgeted manhours were wrong. If events do exist, say for time-period P3, it is necessary to understand how and why they could or have caused disruption to the works. Also, it is necessary to check if notices were sent to the employer citing disruption to the works in P3. This will help the contractor to assign plausible events to the disrupted works which were disrupted in P3.
The fourth step is to determine the delta value between earned and actual curves for P3. In this context and with the help of reliable records, it should be possible to populate how the actual hours were spent by the contractor in this period. Any hours which are solely liable to the contractor must be isolated from delta value, say, idling men waiting for correct shop drawings or non-availability of scaffold material. In addition, a suitable factor for inefficient working as per industry standard may also be deducted from the overall disrupted hours. Adopting these steps will help provide a credible earned value analysis to arrive at the true disrupted hours. In most cases, within the contractor’s disruption claim, the effect of disruption is equal to the delta between total planned and actual value. It is easy to see why it could be construed as a global claim which is devoid of any cause-and-effect argument.
The two commonly used methods for disruption analysis are earned value analysis and measured mile approach
SP: You mentioned the ‘measured mile’ approach; can you tell us more about that?
PO: The measured mile approach involves the comparison of productivity rate achieved for periods when work was not impacted by disruption events (this being the ‘measured mile’) to the productivity rate on identical activities or periods impacted by the disruption events. The ‘measured mile’ calculation is the ratio of impacted and unimpacted productivity rates within the same project. It is the preferred approach since it removes the planned (budgeted units) effort (which could be disputed by the parties) from the disruption calculation. However, the approach could be limited when (a) there is no affected area /period or (b) the affected period is too abrupt to provide a reliable measured mile (c) no similar activities exist to allow for a like-for-like comparison, and (d) no contractual entitlement to compensation exists.
In Amey LG Ltd v Cumbria County Council, Judge Stephen Davies noted that:
- “what is referred to as the ‘measured mile’ approach, . . . ought to have been verified by being able to demonstrate that the planned outputs had actually been achieved in some cases where the disrupting events did not occur . . . it ought to have been relatively easy, by reference to the contemporaneous records which were produced, to have conducted a cross-check on a suitable sample basis. It seems to me that it would . . . have been a reasonably easy exercise to demonstrate this . . . to undertake an appropriate sampling exercise, which would have ensured that any risk of individual variations would have been picked up and catered for.”
As with the previous method, the first task is to identify the disrupted trade and the second task is to plot the actual productivity indices for the work. In the example shown below for piping works, the blue curve shows the actual cumulative progress for the piping works. In contrast, the golden curve is the productivity index, which is calculated as the ratio of actual hours expended to the work output (for example, units installed). The dotted golden line is the trend line for the productivity index for the piping works. A low productivity index is proof (though not absolute) of cost overrun to perform the works, which could be attributed to various reasons, but is not absolute proof of disruption.
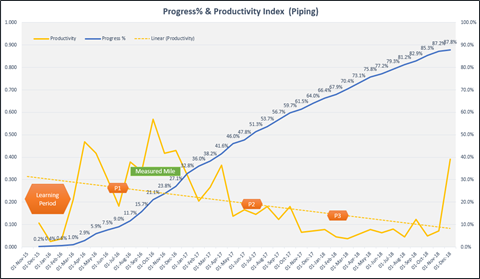
What does the figure tell us about disruption? The portion above the trend line shows periods where productivity for the work was better in relation to other periods which are below the trend line. As is evident, this method does not take into consideration the budgeted hours to arrive at the disrupted hours; rather, it relies solely on actual performance. In this method, the comparison of productivity over periods of time helps to establish periods of time which were likely to have been adversely affected by events. In this case, there are three distinct periods (P1, P2, P3) where productivity falls below the trend line; the initial learning period is ignored. The unimpacted period of performance above the trend line is the ‘measured mile’, which is used as the yardstick to establish what the contractor’s cost performance should-have-been or would-have-been (to establish a base productivity rate). Under the measured mile approach, the entire productivity hours lost within the three periods are in theory claimable based on disruption events that exist in those periods. However, as previously stated there are deductions to be made; firstly, any hours which are solely liable to contractor issues must be segregated and after that, a suitable factor must be applied for the contractor’s inefficient working.
The measured mile is not always a go-to or adopted method for various reasons. If the contractor has not maintained site records, then establishing a base productivity level will not be possible. Also, if the disruption was severe through the course of the project or works, there may be no undisrupted measured mile to compare with. In other cases, if the works are complicated, there may be no typical section to allow a like-for-like comparison of the productivity levels for the works carried out.
SP: Can you encapsulate the most important points?
PO: Yes, in summary, it is advisable to adopt a rational approach for disruption analysis wherein it is necessary to understand the circumstances surrounding disrupted working and choose a suitable method to evaluate the effect of disruption. The two commonly used methods for disruption analysis are earned value analysis and the measured mile approach. However, no one size fits all. The right method must inevitably be adopted to illustrate disruption to the works wherein care must be taken to avoid a global approach. In any event, the availability of records to identify disruption events and daily logs to measure disrupted manhours is a vital ingredient to any successful disruption claim.